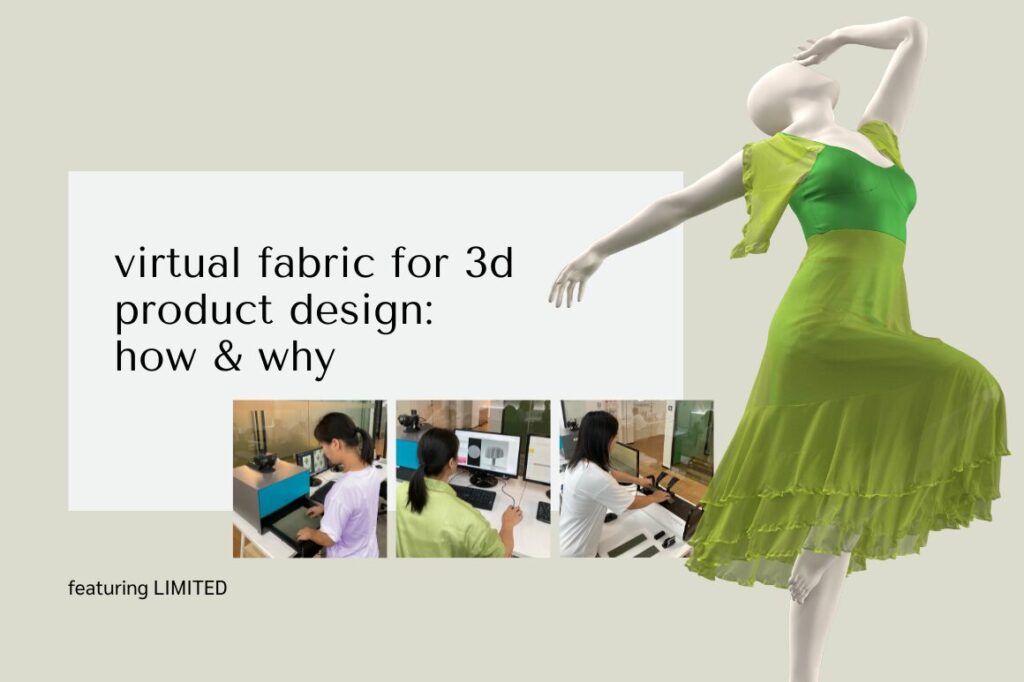
3D technology in design and manufacturing is gaining widespread recognition. Retailers and fashion brands recognize the importance of 3D technologies and their growth potential.
Besides accelerating the product to market time, it also provides an opportunity for apparel product development and manufacturing to be fully digitized. This will enable sustainable production processes.
The ultimate scenarios depict a fashion designer who is confident enough to use 3D technology from the very beginning of the design process. As part of this process, there would be fast decision-making, testing and adjustments of fabrics and colours, collaborating with vendors on ideas, and performing the entire product development lifecycle in 3D in hours instead of days or weeks.
Virtual fabric: How do you get it?
It is important to use accurate fabric virtualization in 3D product design prior to the digital design processes, such as creating patterns and virtual prototypes, style testing for physical prototypes, and finally, creating a virtual showroom. Accurate virtual fabric can help achieve the correct appearance when dressing up different styles and models. It can also help all parties evaluate the correct fit by previewing the pressure and tension map and adjusting the pattern accordingly in Vstitcher to instantly improve and perfect the fitting before a style test.
Digital fabrics can lead to greater fashion industry efficiencies by reducing designers’ reliance on physical samples. It can speed up the design process and provide more opportunities for exploring creative ideas in less time.
To obtain an accurate virtual fabric, it is necessary to use physics and textural data derived from two separate machines: Browzwear’s fabric analyzer (FAB) is able to determine fabric physics, including thickness, stretch, and bend. And Vizoo machine XTex captures texture and fabric structure.
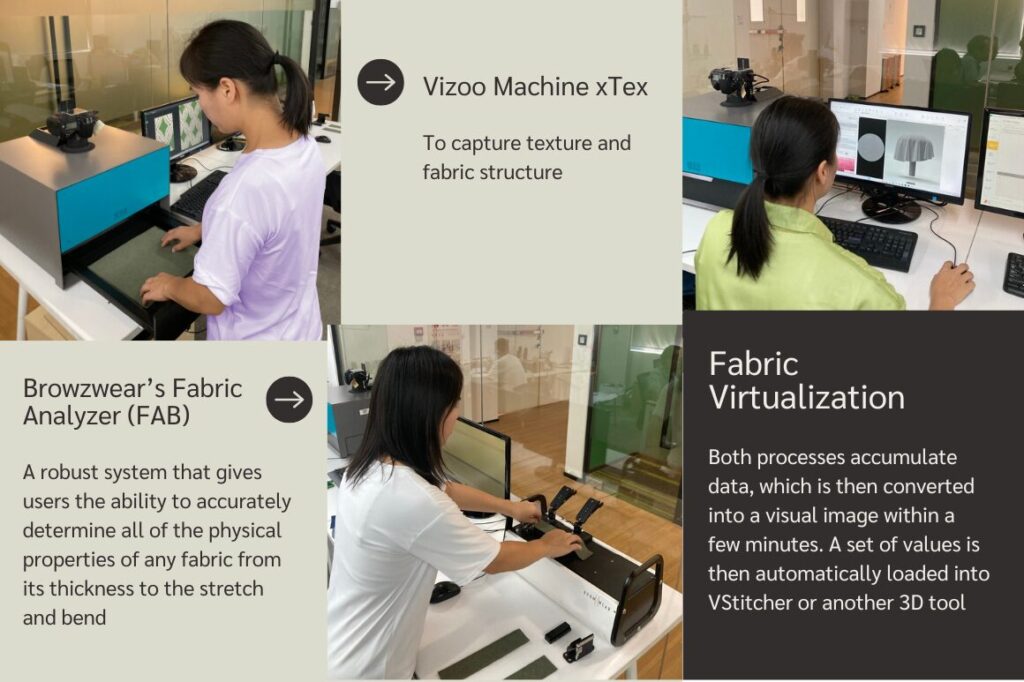
The creation of virtual fabric is dependent on three elements, physics, texture, and data. There will be basic maps to enhance the visual of material texture in 3D. Several layers make up the visual of the fabric in 3D.
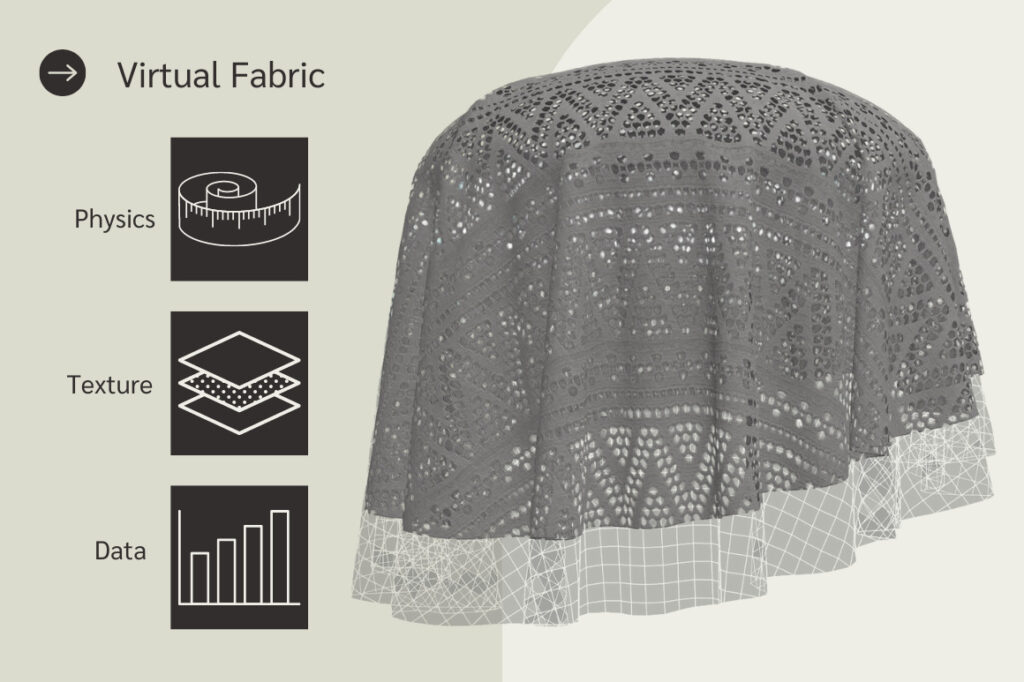
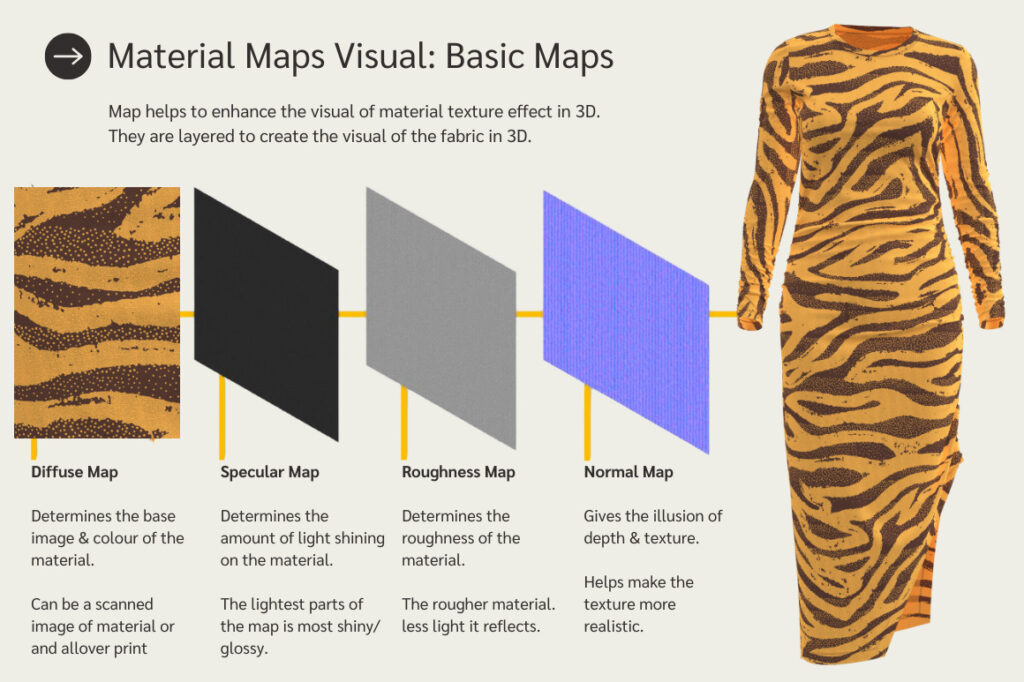
Virtual fabrics have been imported into a virtual fabric library. This is a much more comprehensive library that captures all virtual fabrics and data specifications. Designers can select virtual fabrics and plug them directly into Vstitcher to create 3D styles. Compared with traditional sampling and approval processes, digital fabrics enable designers to experiment more efficiently with colours, prints, and graphics.

Using virtual fabric as part of your 3D product design cycle, what will you be able to accomplish?
1) A virtual style’s fitting appearance can be altered by adjusting the virtual fabric weight
Upon analyzing the physics, there will be a different outcome on design and give the designer and customer a better idea of how the outfit will lay and what kind of shape it should have.
The fabric here is heavier and can be laid closer to the body due to its weight.

2) Achieving True-to-life drapes
It is a very important in constructing a virtual garment, as it helps the designer to apply creativity, and have a sense of how the fabrics blend to create the final style.
For example, to design dress styles, it is imperative to have a high degree of virtual fabric accuracy, particularly when it comes to drape fabrics. There is allowing the customer and designer to determine how the appearance and depth of the drape will appear on the body to make a quick decision whether or not to alter the length or ruffle, and the designer can obtain a clear idea of how the dress will look before stitching or cutting it out.
Here’s how different physics affect drapes of the same size:
(1) 81% nylon 19% spandex virtual powernet fabric 109gsm
(2) fabric weight increased to 366gsm based on virtual powernet fabric
(3) change to 100% polyester virtual shearling fleece 366gsm
Increasing the virtual fabric weight within the same fabrication (from option 1 to option 2) causes the fabric and style to appear more draped, resulting in a longer length for the same dress.
From option 2 to option 3, changing to stiffer and thicker material in the same fabric weight will lower the fabric drapes, resulting in a wider appearance on the shape and ruffles, and shorter body length.

3) Surface design by fabric base decision making
Virtual fabrics accurately reflect their physical and visual properties. Digital twins streamline production processes for physical products. The fabric must be represented by a digital twin that is precise and creatively designed.
Creative and commercial decisions can be made accurately, and with confidence.
Digital fabric creation has to be fast, accurate & cost-effective.
Offering a specific size of fabric swatch (i.e., minimum 25 cm x 30 cm) for generating a virtual fabric. A realistic virtual fabric is essential for displaying the correct structure and allowing customers to easily select the perfect fabric for their design.

4) Accurate virtual fit
An accurate virtual fabric is necessary to assist in evaluating fit, as the fit will be varied by fabric physics, including thickness, stretch and bend. With the use of Vstitcher Browzwear, the company is able to meet the needs of the entire size range. Upon rendering, a digitized human model will be produced and integrated into an online store. This is so customers can select basic measurements and desired body shapes. Meanwhile, the fit can be improved and harmonized in the global fit database to facilitate the setting up of the collection in accordance with the specific size range and shape. In addition, there is a time-saving aspect as well as consistency in size and fit.
The accuracy of sizing facilitates the reduction of returns as well as the prevention of bracketing, a practice in which shoppers purchase items of different sizes because they are unsure which one will fit them.

5) True-to-Life 3D Simulations: Photorealistic rendering
It is important that an accurate virtual fabric is provided for eCommerce in order to display realistic styles for style testing prior to making a purchase decisions by the customer. The style can reduce time-to-market.
Following the virtualization of the fabric, the designer selects the fabric and designs the 3D style. Once the fit evaluation has been streamlined and the virtual style design has been finalized, one test sample is produced for the purpose of style review and serves as a pre-production sample.
Final steps are being taken to dress up the virtual style on a digital human model in order to obtain photorealistic renderings. It is unnecessary to process physical samples in all colorways (plain and prints). A customer can preview the style with various colorways, as well as zoom in to see the virtual fabric. This enhances the preferences of the customers.
This allows the company to test the style immediately before ordering and production, which will reduce marketing expenses, eliminate inventory for over-booking, and reduce return rates.
In view of this, a realistic virtual fabric is of great importance in evaluating fit, as well as identifying style and design preferences from customers.

To learn more about fabric virtualization and hands-on experience to demonstrate and create virtual fabric, visit our website to book a free appointment.